Efficiency in PVC injection moulding is crucial for optimizing production processes and ensuring high-quality outputs. In the competitive landscape of manufacturing, enhancing the efficiency of your PVC injection moulding machine can lead to significant cost savings, improved product quality, and increased profitability. This article will provide a comprehensive guide on how to achieve better efficiency with your PVC injection moulding machine, covering various aspects from machine settings to material quality and environmental conditions.
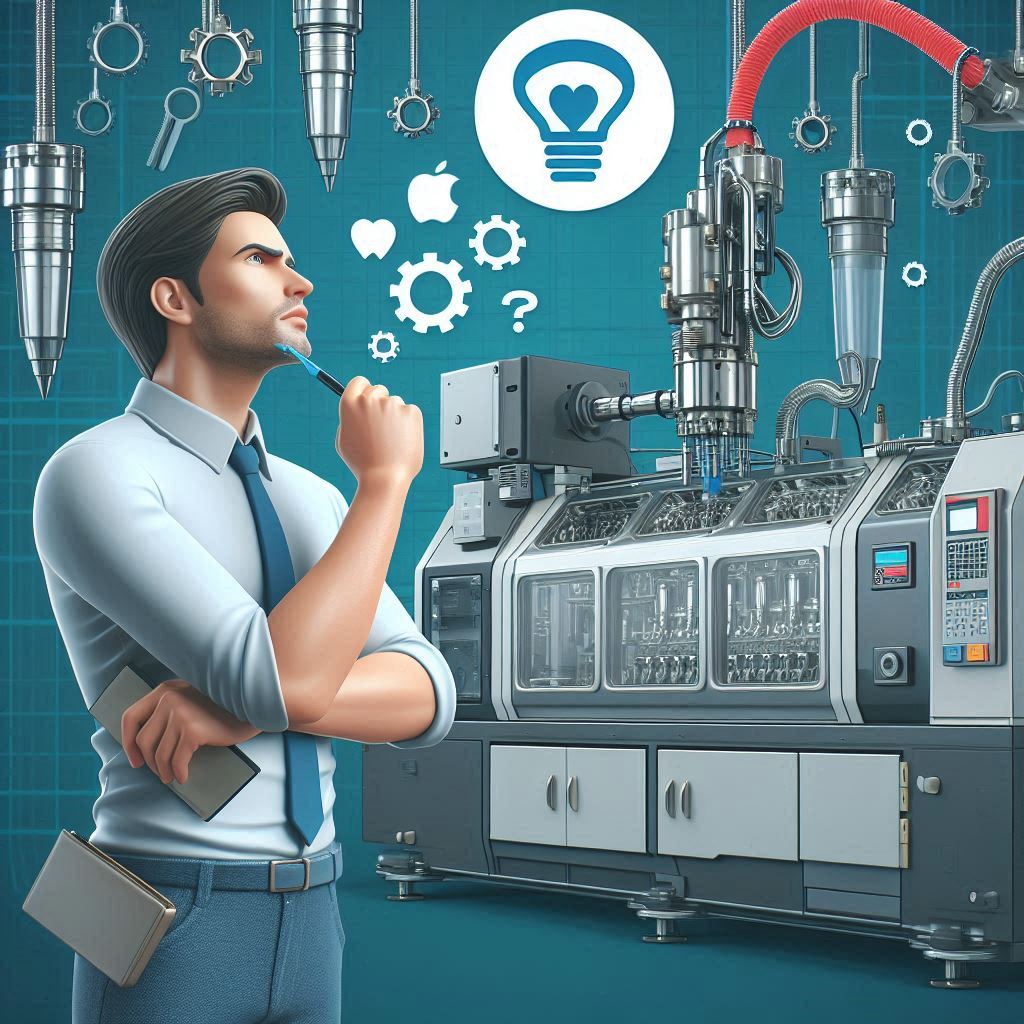
2. Understanding PVC Injection Moulding
What is PVC Injection Moulding?
PVC injection moulding is a manufacturing process where polyvinyl chloride (PVC) is melted and injected into a mould cavity to form various plastic parts. The process is widely used due to PVC’s versatility, durability, and cost-effectiveness. The moulding process involves heating the PVC resin until it becomes a liquid, injecting it into a mould under high pressure, and then allowing it to cool and solidify into the desired shape.
Key Components of a PVC Injection Moulding Machine
A typical PVC injection moulding machine consists of several key components:
- Injection Unit: This includes the hopper, screw, and barrel, which are responsible for melting and injecting the PVC material.
- Clamping Unit: This part holds the mould in place during the injection process and ensures proper alignment.
- Mould: The mould is the cavity that gives the final shape to the injected PVC material.
- Control System: This system manages the machine’s operations, including temperature, pressure, and timing.
3. Factors Affecting Efficiency
Machine Settings and Adjustments
Proper machine settings are crucial for efficient PVC injection moulding. Key settings to consider include:
- Temperature: Ensure the barrel temperature is set correctly for the specific PVC grade being used.
- Injection Pressure: Adjust the injection pressure to avoid overpacking or underpacking of the mould.
- Cycle Time: Optimize the cycle time to balance speed and quality.
Material Quality and Preparation
The quality of PVC resin significantly impacts the efficiency of the moulding process. Consider the following:
- Resin Purity: Use high-quality, pure PVC resin to prevent defects and machine issues.
- Granule Size: Ensure the granules are consistent in size to maintain a uniform melt.
Mould Design and Maintenance
A well-designed and maintained mould is essential for efficient production:
- Design Considerations: Ensure the mould design allows for efficient filling, cooling, and ejection of the part.
- Regular Maintenance: Perform routine inspections and maintenance to avoid defects and downtime.
Environmental Conditions
Optimal environmental conditions can enhance machine performance:
- Temperature Control: Maintain a stable factory temperature to prevent fluctuations that can affect the moulding process.
- Humidity Control: Control humidity levels to prevent material moisture issues.
4. Optimizing Machine Settings
Temperature Control
Maintaining the correct temperature is vital for achieving a consistent melt. Regularly calibrate the temperature sensors and ensure proper heating and cooling mechanisms are functioning effectively.
Pressure and Speed Adjustments
Adjust injection pressure and speed based on the specific requirements of the part being produced. Monitor these settings closely to prevent issues such as short shots or flash.
Calibration and Maintenance
Regular calibration and maintenance are essential to keep the machine running efficiently. Follow the manufacturer’s maintenance schedule and address any anomalies promptly.
5. Enhancing Material Quality
Selecting the Right PVC Resin
Choose the appropriate grade of PVC resin based on the requirements of the final product. Factors such as impact resistance, flexibility, and color should guide your selection.
Proper Storage and Handling
Store PVC resin in a dry, cool place to prevent moisture absorption. Proper handling practices can also reduce contamination and ensure consistent quality.
Pre-processing Techniques
Use pre-processing techniques such as drying the resin to remove moisture before injection. This can help prevent defects and improve the quality of the final product.
6. Improving Mould Design
Design Considerations for Efficiency
Design the mould to facilitate easy flow of the PVC material and efficient cooling. Incorporate features such as vents and cooling channels to enhance performance.
Regular Inspection and Maintenance
Conduct regular inspections of the mould for signs of wear and tear. Perform necessary repairs and maintenance to avoid production delays and quality issues.
7. Environmental Conditions
Optimal Factory Conditions
Ensure the production environment is well-maintained, with stable temperature and humidity levels. This can prevent issues such as material degradation and machine malfunctions.
Ventilation and Humidity Control
Proper ventilation and humidity control can help maintain consistent material properties and prevent issues such as condensation.
8. Implementing Automation
Benefits of Automation
Automation can enhance efficiency by reducing manual intervention, increasing precision, and improving consistency. Consider integrating automation systems to streamline your production process.
Types of Automation Systems
Explore various types of automation systems, including robotic arms, conveyor systems, and automated quality control systems. Choose systems that align with your production needs.
Integration with Existing Systems
Ensure that new automation systems can be seamlessly integrated with your existing moulding equipment. Proper integration can maximize efficiency and minimize disruptions.
9. Monitoring and Analyzing Performance
Key Performance Indicators (KPIs)
Track KPIs such as cycle time, defect rates, and machine downtime to assess the efficiency of your moulding process. Use these metrics to identify areas for improvement.
Using Data for Continuous Improvement
Analyze performance data to identify trends and areas for improvement. Implement changes based on data-driven insights to enhance overall efficiency.
10. Case Studies and Expert Insights
Real-World Examples of Efficiency Improvements
Examine case studies of companies that have successfully improved their PVC injection moulding efficiency. Learn from their strategies and results.
Expert Quotes and Recommendations
Consult with industry experts to gain insights and recommendations on improving efficiency. Their expertise can provide valuable guidance for optimizing your processes.
11. Future Trends in PVC Injection Moulding
Technological Advancements
Stay informed about technological advancements in PVC injection moulding, such as new materials, process innovations, and machine upgrades. Embrace these advancements to maintain a competitive edge.
Emerging Best Practices
Adopt emerging best practices to enhance efficiency and sustainability in your moulding processes. Keep abreast of industry trends and continuously update your practices.
12. Practical Tips for Daily Operations
Daily Maintenance Checklist
Follow a daily maintenance checklist to ensure that your machine operates smoothly. Include tasks such as checking fluid levels, cleaning the machine, and inspecting for wear and tear.
Quick Fixes for Common Issues
Learn quick fixes for common issues such as nozzle blockages or uneven cooling. Addressing these problems promptly can prevent production delays and maintain efficiency.
13. Conclusion
In conclusion, improving the efficiency of your PVC injection moulding machine involves optimizing machine settings, enhancing material quality, refining mould design, and managing environmental conditions. By implementing these strategies, you can achieve significant gains in productivity and product quality. Stay informed about technological advancements and best practices to continuously enhance your efficiency.